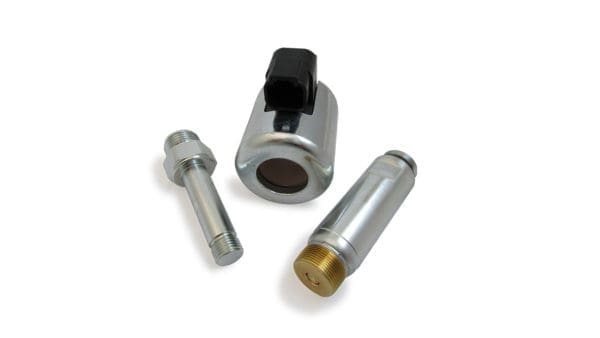
For decades, Lisk has been engineering and manufacturing solenoids for a variety of mobile hydraulic applications. Solenoids offer a robust and reliable solution for difficult environments seen in mobile hydraulic applications such as construction, agriculture, mining and material handling.
Before deciding on a solenoid for a particular mobile hydraulic application, there are a number of points which should be considered to ensure the optimal solenoid is designed. The following points all influence the proper selection and should be given careful consideration.
-
How is the valve intended to function? Will it simply be an open/close type application, or will the application need finite control. Solenoids are grouped into two basic categories, On/Off or Proportional.
On/Off solenoids: A solenoid that only has two power based operating conditions in the valve, fully powered or unpowered. There is no intermediate operating state, the valve has either 100% flow, of zero flow.
Proportional solenoids: A solenoid that has a variable range of operating conditions based on the amount of input power. This allows the valve to have a near infinite range of flow from zero to 100%, which provides precise control of components.
-
The total movement expected of the solenoid when electrical power is applied. It is also often define as the air gap between movable plunger and the fixed pole piece in the de-energized condition. For the greatest efficiency and smallest size, design for the shortest stroke possible. When a given amount of “work” is required, try to use a short stroke/high force combination rather than longer strokes and lower forces.
-
The basic function the solenoid is to perform:
Pull force: when energized the plunger retracts pulling the load. De-energized, the plunger is extended the specified stroke distance.
Push force: When energized, push rod extends pushing the load. A push solenoid is actually a pull solenoid with the addition of a push rod which rides against the internal face of the plunger.
Hold force: Plunger is pulled in either electrically or by external force and contacts the pole pieces. With power applied, the plunger remains fixed resisting the external pull or push load.
Combination: Two or all three of these functions can be combined in one solenoid
-
The majority of modern solenoids create a pressure vessel when installed on a valve, and have ratings up to 5000 PSI and higher. Old technology used valve shaft seals which isolated valve pressure from the solenoid plunger cavity. A potential source of valve failures – leaking dynamic seal – is eliminated. Valve reliability improves. Also without the shaft seal, the total force required of the solenoid to actuate the valve is reduced by the pressure differential force across the seal and the seal to shaft friction force. In many cases, the elimination of these two forces make it possible to use a smaller size solenoid.
-
The load the solenoid is capable of pulling, pushing, or holding at a specified stroke when energized under a specific set of conditions: of voltage or current, temperature, and duty cycle.
-
A comparison of the time a solenoid is energized to the time it is de-energized, expressed as a percentage:
DUTY = (ON time)/(ON Time + OFF time) x 100
For a given force/stroke requirement, the smaller the duty cycle percentage, the smaller the solenoids.
Intermittent Duty- Solenoid ON for only a short time, usually not more than 2 or 3 minutes, then followed by an OFF time which is normally at least as long as the ON time. This ON and OFF cycling can be repated continuously over total life of the solenoids. AS the ON time decreases and the OFF time increases, more current can be applied to the solenoid without causing coil overheating. By being able to use larger current drain (increased power), a smaller size solenoid can be selected to product the same force/stroke output.
Pulse Duty: An intermittent duty unit with extremely short ON time. A duty cycle normally in the 10% range. Maximum input power for a size solenoids.
Continuous Duty: Solenoid ON continuously without interruption for periods of about 30 minutes or longer. Proportional solenoids are typically designed for continuous duty applications.
With no OFF time to allow the coil to cool, continuous duty solenoids must have coils wound to limit the current drain and must also be large enough to provide for adequate heat radiation to prevent coil burn-out. This means that a continuous duty solenoids will be considerably larger than an intermittent design to produce the same force/stroke.
One way to get around the continuous duty unity size problem is to go to a two coil work/hold design.
-
For applications where solenoids must be energized for long periods in the hold position but where physical size and weight of the continuous duty solenoids present a problem, two coil designs offer ideal solutions. The two coil units combine the smaller size advantage of an intermittent solenoid with the lower power consumption of the continuous duty design. The work or pull in coil operates at the high power levels of the intermittent duty solenoids and moves the load through the complete stroke. At end of the stroke, the second or hold coil is added to the circuit. The two coils together hold the load continuously at a power level which, in most cases, is substantially below that of the conventional single coil continuous duty solenoid. The “adding” of the second coil can be accomplished by a switch mounted within the solenoid or by remote externally mounted switch supplied as separate item.
-
Ambient temperature of wire in the coil winding. It is the combination of ambient coil temperature plus heating due to current flow through the coil.
Ambient Temperature: the stable coil wire temperature with no electrical power to the solenoid.
Heat Rise: The maximum stable increase in coil wire temperature during solenoid operation at rated voltage and duty cycle in designed ambient conditions.
Stabilized Temperature: The final stable temperature the coil wire reaches during operation – ambient temperature plus coil heat rise.
-
Solenoid force is generated by the amount of ampere turns the coil produces. Ampere turns is calculated by the coil current draw times the number of wire turns.
On/Off solenoids: For any given stroke, solenoid force decreases with coil temperature increase and conversely, increases when coil temperature is lowered. This is the result of changes in coil wire resistance with changes in wire temperature. The higher the wire temperature, the higher the resistance will be. Since ON/Off solenoids are powered by voltage, the amount of current available is calculated as Voltage divided by Resistance. As the coil resistance increases the current draw decreases and conversely as the coil resistance decreases the current draw increases.
Proportional solenoids: For any given stroke, solenoid force remains constant even as coil temperature changes. This is because proportional solenoids are powered by current instead of voltage. The amount of current available is only limited by the voltage supply. Voltage is calculated by Current multiplied by the Resistance. As the coil resistance increases the amount of voltage needed to maintain the given current increases, conversely as the coil resistance decreases the voltage draw decreases.
-
Time, usually in milliseconds, from the points at which power is applied until the plunger reaches the end of its design stroke. Two main factors contribute to the overall response time. One is time it takes the current to overcome coil inductance and develop required magnetic flux field. The other is the time it takes for the plunger to actually travel the stroke distance. Flux build up normally takes more than half of the total response time. Generally speaking, the response time varies between 5 milliseconds for small size units at short strokes up to about 250 milliseconds for long stroke, larger sizes.
To achieve faster response times the solenoid must be over-powered. A solenoid size must be selected which will produce a force at the start of the required stroke several times as large as would be needed under normal speed operation. Also, stroke should be as short as possible to keep plunger travel time at a minimum. Special high speed design capability is available at Lisk.
-
On/Off: Current = Power (catalog value)/ Voltage (as specified)
Proportional: Current = (catalog value)
-
On/Off: Resistance = Voltage (as specified) / current (as determined above)
Proportional: Resistance = Voltage (as specified) / Current (as specified)
In operation, the coil resistance will increase due to the heating of the coil wire.
-
Solenoids can be designed to meet a variety of operational condition requirements such as Humidity/Water Splash, Oil spray/immersion, sand, dust, dirt, temperature, and shock/vibration.
POTENTIAL SPECIAL MODIFICATIONS
Special plunger ends
Return Spring (pull or Push)
Internal: Spring inside solenoids body between plunger and pole piece.
External: Spring fits over special length plunger and is held captive between nose boss and retainer at the end of the plunger.
-
Provides simultaneous pull and push output during a single plunger stroke. These units offer a primary pull or push force plus a lower force, secondary output in opposite directions.
-
Push pull designs are basically separate solenoids in one body with a single output connection. When one coil is energize, the unit pulls or pushes the design stroke and force. The solenoid then remains in that position until the other coil is energize, moving the output connection the same distance in the opposite direction with the same force.
-
To prevent residual magnetism from holding plunger and pole pieces together after power to the solenoid is cut off and also to achieve minimum drop out time where fast response is required, several features are available. These include external ring, internal ring, shimmed pole face, plunger pin, retained plunger (end cap, stop nut, snap ring, plunger pin)
-
Push Units: Plungers can be made longer, have special machining on external end or have buttons added to meet specific application needs.
Pull Units: A standard diameter, fixed push rod with pull button added is normally furnished. Button diameter about the same as solenoid body. Rod length to suit application. Depending on the application shapes other than button can be mounted to rod for pulling.
-
There are several types of termination possible including varying length lead wires (most connector variants can be added to the lead wires), integrated AMP/Weathpack, Deutsch, DIN, spade terminal block, screw terminal block, conduit receptacle, and more.
-
Several design consideration not previously mentioned include plunger anti-rotation, plunger impact absorber, and sound deadening.
Lisk’s engineers are adapt at solving difficult application problems and can work collaboratively with you to determine the best possible solenoid solution for your application. Contact us to get started on your next project.